Fiber Optic Splicing & Termination
In today’s high-speed digital world, fiber optic networks serve as the backbone of telecommunications, internet infrastructure, and data transmission systems. Ensuring seamless connectivity and minimal signal loss is critical, which is why fiber optic splicing and termination are essential processes in network installation and maintenance.
Splicing and termination directly impact the performance, reliability, and longevity of fiber optic networks. Whether extending fiber connections, repairing damaged cables, or integrating new components, choosing the right technique can make a significant difference in signal integrity and overall network efficiency.
What Is Fiber Optic Splicing & Termination?
Fiber optic splicing and termination are crucial techniques used in the deployment and maintenance of fiber optic networks. These processes ensure that fiber optic cables are properly connected, minimizing signal loss and maximizing network efficiency.
The Importance of Splicing & Termination in Network Reliability
A well-implemented splicing and termination strategy directly impacts the performance and longevity of fiber optic systems. Poorly executed connections can lead to signal degradation, increased maintenance costs, and network downtime.
Key reasons why proper splicing and termination are essential:
- Signal Integrity: Ensures minimal loss and high transmission quality for voice, data, and video applications.
- Network Longevity: Proper techniques prevent physical damage and environmental wear, extending the lifespan of fiber infrastructure.
- Scalability: Enables seamless network expansion by securely integrating new fiber connections.
- Reduced Downtime: Reliable connections decrease the likelihood of performance issues and costly repairs.
Both splicing and termination require precision, industry-standard techniques, and specialized equipment to achieve optimal performance. The choice of method depends on factors such as the type of network, environmental conditions, and long-term maintenance requirements.
Types of Fiber Optic Splicing
Fiber optic splicing is the process of permanently or semi-permanently joining two fiber optic cables to ensure uninterrupted data transmission. There are two primary methods of splicing: fusion splicing and mechanical splicing. Each technique has distinct advantages and is used based on network requirements and environmental conditions.
Fusion Splicing
Fusion splicing is the most commonly used method for creating a permanent connection between two fiber optic cables. This process involves using an electric arc to melt and fuse the ends of two fibers, forming a seamless, low-loss connection.
How Fusion Splicing Works:
- Fiber Preparation: The protective coating is stripped from the fiber, and the bare glass is cleaned.
- Cleaving: The fiber is precisely cut using a fiber cleaver to ensure smooth, perpendicular end faces.
- Alignment: The fiber cores are aligned using a fusion splicing machine, ensuring optimal connectivity.
- Fusing: An electric arc is applied, melting the fiber ends and fusing them into a single, continuous strand.
- Protection: The splice is secured with a heat-shrink sleeve to protect it from environmental damage and mechanical stress.
Benefits of Fusion Splicing:
✅ Low Signal Loss: Provides the lowest insertion loss, ensuring high-quality signal transmission.
✅ Strong & Durable: Creates a permanent, highly reliable bond resistant to environmental factors.
✅ Ideal for Long-Distance Networks: Best suited for high-bandwidth and long-haul fiber optic installations.
Best Practices for Fusion Splicing:
- Use high-precision cleavers to achieve clean, smooth fiber ends.
- Keep fiber ends free from dust, oil, and debris to prevent signal loss.
- Regularly calibrate fusion splicing machines for optimal performance.
- Use appropriate splice protection to safeguard against moisture and mechanical damage.
Mechanical Splicing
Mechanical splicing is a quicker, cost-effective alternative that does not require melting the fiber ends. Instead, it relies on precise alignment and an index-matching gel to create a low-loss connection between fibers.
How Mechanical Splicing Works:
- Fiber Preparation: The fiber is stripped, cleaned, and cleaved to create smooth end faces.
- Insertion: The prepared fibers are inserted into a mechanical splice housing.
- Alignment: The splice connector aligns the fiber ends for optimal core matching.
- Securing: The fibers are locked in place using a mechanical clamp, and index-matching gel is applied to minimize light loss.
When to Use Mechanical Splicing:
✔ Quick Repairs: Ideal for emergency restorations and temporary connections.
✔ Low-Cost Installations: Suitable for applications where fusion splicing is not cost-effective.
✔ Short-Distance Networks: Best for situations where high durability and low insertion loss are not critical.
While fusion splicing is preferred for permanent, high-performance networks, mechanical splicing offers a practical alternative for fast, budget-friendly fiber connections.
Fiber Optic Termination Methods
Connectorized Termination vs. Splicing
- Connectorized Termination
- Uses pre-manufactured fiber optic connectors to create a detachable connection.
- Allows easy reconfiguration, testing, and maintenance.
- Commonly used in data centers, telecommunications, and enterprise networks.
- Requires precision polishing and alignment for optimal performance.
- Splicing Termination
- Uses fusion splicing or mechanical splicing to permanently join fiber ends.
- Provides lower insertion loss and higher durability than connectors.
- Best suited for long-haul networks, outside plant installations, and high-performance applications.
- Requires specialized equipment but ensures superior signal integrity.
Choosing the right method depends on factors such as network requirements, cost, and the need for future modifications. Connectorized terminations are ideal for applications needing flexibility, while splicing is better for long-term, high-performance connectivity.
Types of Fiber Optic Connectors
Fiber optic connectors provide a quick and efficient way to terminate fiber cables while maintaining signal integrity. Each connector type is designed for specific applications, offering different levels of performance, size, and ease of use.
Connector Type | Description | Common Applications |
SC (Subscriber Connector) | Square-shaped, push-pull connector with low insertion loss. | Data centers, telecom networks, GPON (Gigabit Passive Optical Networks). |
LC (Lucent Connector) | Small-form-factor connector with a secure latch mechanism. | High-density networking, fiber-to-the-home (FTTH), enterprise systems. |
ST (Straight Tip Connector) | Bayonet-style connector with a twist-lock mechanism. | Industrial applications, multimode fiber networks, legacy systems. |
FC (Ferrule Connector) | Threaded connector providing strong mechanical stability. | High-vibration environments, fiber optic sensing applications. |
MTP/MPO (Multi-Fiber Push-On/Pull-Off) | Multi-fiber connectors used for high-speed, high-density applications. | Data centers, cloud computing, high-speed backbone networks. |
Each connector type plays a crucial role in fiber optic infrastructure, and selecting the right one depends on factors like space constraints, signal performance, and application requirements.
Common Fiber Optic Splicing Challenges & How to Overcome Them
Fiber optic splicing is a precise process that requires careful execution to maintain optimal network performance. However, several challenges can impact the quality and reliability of splices. Understanding these challenges and how to mitigate them ensures a stronger and more efficient fiber optic network.
Splice Loss & How to Reduce It
Splice loss refers to the reduction in signal strength that occurs when two fiber optic cables are joined. Excessive splice loss can degrade network performance, causing increased attenuation and signal distortion.
Causes of Splice Loss:
- Misalignment: Poor core alignment leads to high insertion loss.
- Improper Cleaving: Rough or angled fiber ends prevent a smooth fusion.
- Contamination: Dust, dirt, or oil on fiber surfaces interferes with light transmission.
- Air Gaps in Mechanical Splicing: If fibers are not properly seated in a mechanical splice, signal loss increases.
Ways to Reduce Splice Loss:
✅ Use High-Precision Cleavers – Ensures clean, flat fiber ends for proper fusion.
✅ Maintain Proper Alignment – Automatic core alignment splicers provide the best accuracy.
✅ Clean Fiber Thoroughly – Use alcohol wipes and compressed air to remove dust and oils.
✅ Perform OTDR Testing – Verify splice quality and detect any excessive loss post-splicing.
Environmental Factors Affecting Splicing Quality
External conditions can significantly impact the quality of fiber optic splicing. Unfavorable environmental factors can lead to higher splice loss, cable damage, or network instability.
Key Environmental Factors & Mitigation Strategies:
Factor | Impact on Splicing | How to Mitigate |
Temperature Extremes | Causes fiber expansion/contraction, leading to microbends. | Perform splicing in a controlled environment or use splice enclosures. |
Humidity & Moisture | Can seep into splices, degrading performance over time. | Use sealed splice closures and silica gel packs. |
Dust & Contaminants | Blocks fiber alignment, increasing insertion loss. | Always clean fiber ends before splicing and work in dust-free environments. |
Mechanical Vibration | Shifts fiber alignment during splicing, leading to poor fusion. | Use vibration-dampening mats and ensure stable work surfaces. |
UV Exposure | Accelerates fiber degradation, reducing lifespan. | Use UV-resistant coatings and outdoor-rated splice closures. |
By proactively addressing these challenges, fiber optic professionals can improve splice quality, minimize signal loss, and ensure the long-term reliability of network infrastructure.
Tools & Equipment for Fiber Splicing & Termination
Achieving high-quality fiber optic splicing and termination requires specialized tools and equipment. These tools help ensure precision, minimize signal loss, and maintain the long-term reliability of fiber optic networks. Below are the essential tools used in the splicing and termination process.
OTDR Testing (Optical Time-Domain Reflectometer)
What Is OTDR Testing?
An Optical Time-Domain Reflectometer (OTDR) is an essential tool used to analyze fiber optic cable performance. It detects splice loss, attenuation, and breaks in the fiber by sending light pulses through the cable and measuring the reflected signal.
Why OTDR Testing Is Important:
- ✅ Measures Splice Quality: Identifies splice loss and irregularities in fiber connections.
- ✅ Detects Faults & Breaks: Pinpoints damage, bends, or inconsistencies in the fiber.
- ✅ Verifies Installation Integrity: Ensures proper fiber deployment and identifies potential weak points.
- ✅ Optimizes Network Performance: Helps technicians troubleshoot and maintain fiber infrastructure.
How to Perform OTDR Testing:
- Connect the OTDR to the fiber optic cable.
- Select the Appropriate Test Settings based on fiber length and type.
- Send a Test Pulse through the fiber to analyze reflection and loss.
- Interpret the OTDR Trace to identify splice loss, bends, or fiber breaks.
- Document & Address Issues to ensure optimal fiber performance.
Pro Tip: Always use a launch cable when conducting OTDR tests to reduce “dead zones” in measurement data.
Splicing Machines & Alignment Tools
Splicing machines and alignment tools are critical for achieving low-loss fiber connections. The right equipment ensures precise fiber alignment, smooth fusion, and long-term durability.
Fusion Splicing Machines
Fusion splicers use an electric arc to permanently join two fiber ends. These machines provide the most reliable, low-loss connections for high-performance networks.
- Core Alignment Fusion Splicers – Use cameras to precisely align fiber cores, minimizing splice loss.
- Cladding Alignment Fusion Splicers – Align fibers based on outer cladding, suitable for less demanding applications.
Mechanical Splicing Tools
Mechanical splicing relies on alignment and index-matching gel rather than fusion. Tools used include:
- Mechanical Splice Holders – Secure fibers in place for proper alignment.
- Precision Cleavers – Ensure smooth, even fiber ends for optimal connection.
Fiber Alignment Tools
Accurate fiber alignment is crucial for both fusion and mechanical splicing. Key tools include:
- Splice Alignment Jig: Helps maintain fiber positioning during splicing.
- Fiber V-Groove Holders: Secure fibers in a straight line for precise alignment.
By using the right testing equipment, splicing machines, and alignment tools, fiber optic technicians can ensure optimal network performance, minimal signal loss, and long-lasting fiber connections.
Best Practices for Ensuring Long-Term Performance
Maintaining a reliable and efficient fiber optic network requires careful attention to best practices in splicing and termination. Proper installation, environmental protection, and routine maintenance can significantly enhance network longevity and minimize downtime.
1. Precision in Splicing & Termination
- ✅ Use High-Quality Equipment: Invest in precision cleavers, fusion splicers, and OTDR testing tools to ensure accurate fiber alignment.
- ✅ Ensure Clean Fiber Ends: Always clean fiber ends before splicing or terminating to prevent contamination and signal loss.
- ✅ Proper Core Alignment: Misaligned fiber cores result in excessive signal loss—use core-alignment fusion splicers for best results.
2. Protecting Fiber Optic Splices & Connections
- ✅ Use Splice Enclosures: Always place spliced fibers inside protective enclosures to prevent physical damage and moisture exposure.
- ✅ Minimize Fiber Stress: Avoid sharp bends or excessive tension on fiber optic cables, as this can lead to microbending and performance degradation.
- ✅ Environmental Sealing: Use gel-sealed or heat-shrink splice protectors to shield fibers from dust, moisture, and temperature fluctuations.
3. Routine Testing & Maintenance
- ✅ Conduct Regular OTDR Testing: Periodic OTDR testing helps detect issues before they cause network failures.
- ✅ Inspect Connectors & Splices: Over time, connectors can degrade—clean and replace them as needed to maintain peak performance.
- ✅ Document All Splices & Terminations: Maintain detailed records of fiber splices, locations, and test results to simplify troubleshooting and future expansions.
4. Follow Industry Standards & Best Practices
- ✅ Adhere to TIA/EIA & ISO Standards: Ensure all splicing and termination processes meet industry regulations for quality and performance.
- ✅ Train Technicians Properly: Well-trained professionals are crucial for achieving reliable splices and terminations.
- ✅ Use Compatible Components: Always match fiber types, connectors, and splicing methods to avoid compatibility issues.
Optimize Your Fiber Network with DataField Technology Services
For expert fiber optic splicing, termination, and network optimization, trust DataField Technology Services. Our experienced technicians ensure precision, reliability, and long-term performance for your fiber infrastructure.
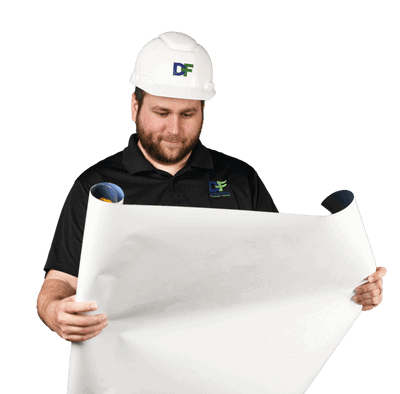